L’intérêt d’un matériau sandwich en infusion :
Un matériau sandwich est l’association d’une âme (mousse, balsa nid d’abeille …) de forte épaisseur et de faible densité et de deux peaux à fortes caractéristiques mécaniques. Les peaux sont souvent un composites de renforts (fibres de verre, carbone etc …) et d’un liant (résine thermo durcissables : poyester vinylester époxy …)
L’épaisseur élevée de l’âme, qui permet d’augmenter l’écartement des peaux, a pour but d’accroître l’inertie du matériaux composites (rigidité obtenue avec moins de renforts structurels) elle peut aussi offrir d’autres avantages (isolation phonique, thermique …)
L’infusion garantit une très bonne adhésion entre les peaux et l’âme ce qui est l’un des points critiques des matériaux sandwich et permet de renforcer quand c’est nécessaire la cohésion de la mousse (pontage entre les peaux).
Un bon sandwich est alors réalisé et on obtient alors un matériaux présentant :
¤ Bonne résistance en cisaillement.
¤Bonne résistance en compression.
¤ Une faible densité.
Coupe d’un sandwich :
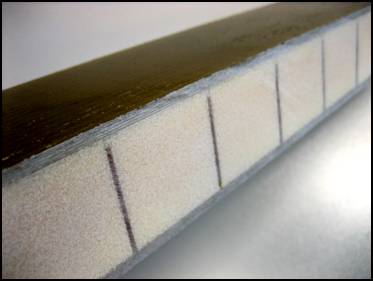
L’INFUSION : un procédé de haute technologie
Le procédé d’infusion consiste à aspirer de la résine à travers un empilement de tissus (renforts structurels) et d’ame (éventuellement) placés entre un outillage (moule) et un film plastique. Pour cela un vide généralement compris entre 0,6 et 0,95 bar est effectué à l’aide d’une pompe à vide.
Ce procédé est notamment conseillé pour les grandes pièces et permet de réaliser des matériaux composites sans que le personnel ne soit en contact avec les résines (amélioration notables des conditions de travail en terme d’hygiène et de protection de l’environnement pas de solvants dans l’air) en outre, le délai possible au cours du drappage permet la mise en place de procédures qualité (contrôle du nombre et du choix des renforts) .
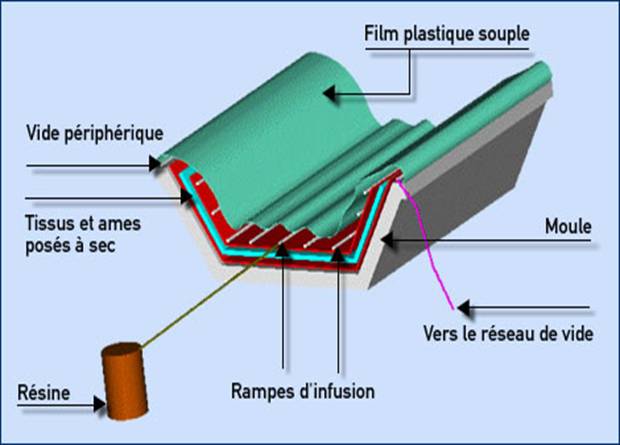
Si le principe de l’infusion ainsi énoncé parait simple, le process d’infusion est en fait complexe par le très large éventail de paramètres influant sur la réponse :
¤ les caractéristiques dimensionnelles et mécaniques de la pièce finale et de son moule
¤ le choix des matériaux : type d’ame et de renforts structurels et leur perméabilité, choix de la résine et sa viscosité (contrôle de la température)
¤ le choix et les méthodes de mise en place des périphériques spécifiques à l’infusion :
¤ rampe de drainage du vide
¤ rampe de distribution de la résine
¤ matériaux drainant associés
TREGOR COMPOSITES utilise la méthode de l’infusion à chaque fois qu’elle est possible !
Par webfastnet.free.fr